
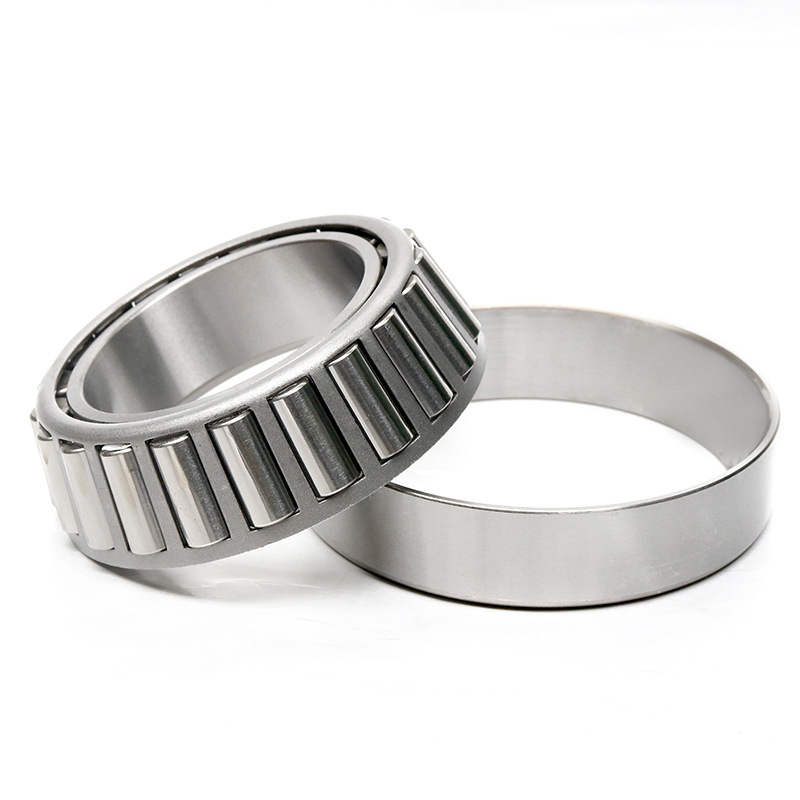
The journey behind creating high-performance precision bearings involves an elaborate set of processes, starting right from the selection of raw materials up to the final packaging. The emphasis on adhering to stringent quality norms ensures that each bearing serves its purpose efficiently, especially for automotive and motorcycle applications.
Raw Material Selection
The cornerstone of manufacturing precision bearings lies in selecting superior raw materials. High-quality materials like stainless steel and ceramic are commonly used due to their resilience and durability. Sourcing these materials involves rigorous initial quality checks to ensure they meet predefined standards. Only materials passing these checks proceed further into production.
Initial Forming and Shaping
Once the appropriate materials are selected, they undergo forging and casting processes to form initial shapes. Advanced machinery plays a critical role during this phase to maintain accuracy. Techniques like CNC machining help in shaping them precisely, laying a foundation for the subsequent intricate processes.
Heat Treatment
The heat treatment stage is crucial for enhancing the durability of precision bearings. Methods like annealing and quenching stabilize the metal's structure by carefully controlling temperature and time parameters. Monitoring systems ensure consistent results, making the bearings both strong and long-lasting.
Precision Grinding
Precision grinding brings out the best performance from bearings by ensuring exact measurements. Surface and cylindrical grinding techniques produce smooth finishes, minimizing friction when the bearings function. State-of-the-art equipment guarantees unparalleled accuracy during grinding.
Assembly of Components
The assembly process integrates inner and outer rings, rolling elements, and cages meticulously. Using precise techniques ensures flawless fitment, contributing significantly to the bearing's efficiency. Robust quality control mechanisms continually check dimensions and alignment throughout assembly.
Lubrication Application
Lubrication is indispensable for optimizing the bearing's operation by reducing wear and tear. Grease or oil lubricants are typically employed, depending on the application requirements. Sophisticated application methods ensure even distribution and ample coverage, extending the component’s service life.
Quality Assurance and Testing
A multi-tiered quality assurance regimen tests the bearings' dimensional accuracy, load endurance, and overall reliability. Comprehensive testing determines if they stand up to strenuous conditions over prolonged use. Compliance with industry certifications substantiates their dependability in automotive and motorcycle applications.
Cleaning and Packaging
The final steps involve thorough ultrasonic cleaning to eliminate contaminants, followed by anti-corrosion treatments. Proper packaging safeguards the bearings against damage during transport. This meticulous attention to detail ensures you receive flawless, ready-to-use components every single time.
Innovations and Technological Advancements
Recent innovations have revolutionized the manufacturing landscape. Automation and robotics streamline operations while Industry 4.0 technologies enhance predictive maintenance capabilities. Such advancements translate to higher productivity, greater consistency, and better scalability in producing these top-tier precision bearings.
Environmental Considerations
Sustainability practices are increasingly integral to modern manufacturing. From responsibly sourcing raw materials to effective waste management and adopting energy-efficient processes, conscientious manufacturers reduce environmental impact while adhering to green principles.